Every now and again I manage to learn from a previous mistake and do it right the next time. In this case I realized that it would be much easier to pre-finish the slats than to finish them after assembly. I also realized that I might want to use different finishes for the slats, since they're maple and the rest is cherry. I decided to spray them with water-based lacquer --
Target Coatings makes a fantastic product called
USL. Water-based finishes are nice because they clean up easily, are non-toxic, and safe to spray without crazy equipment (like "explosion-proof exhaust fans".)
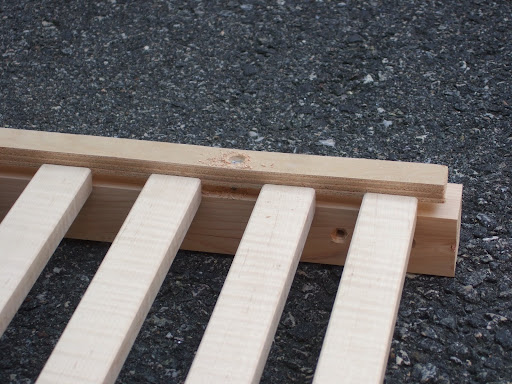
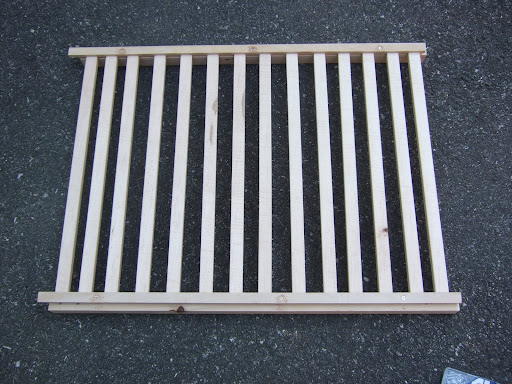
In order to make spraying easy I came up with this set-up: the slats are held in a frame made of scrap wood. I can easily spray them all at the same time, but then disassemble it to sand between coats. In addition, the scrap pieces cover the tenons so that they don't get finish on them.
I started out with a thinned-out coat to seal the wood and penetrate for better "popping" of the grain. I also added a tiny bit of
aniline dye stain (from J.E. Moser's) directly to the finish to compensate for a common problem with water-based finished -- unlike solvent-based finishes, they impart no yellow color and can make wood look cold.
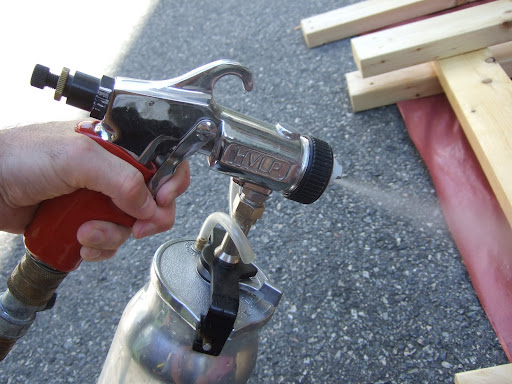
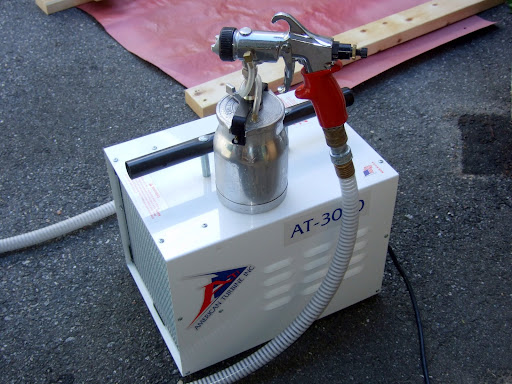
I sprayed a total of four coats of USL using my
HVLP (high-volume, low-pressure) spray system. I bought a 3-turbine machine several years ago from
American Turbine -- it was pretty expensive considering that it's basically a glorified vacuum cleaner with a hose and a spray gun attached. The lacquer goes on easily and dries fast.
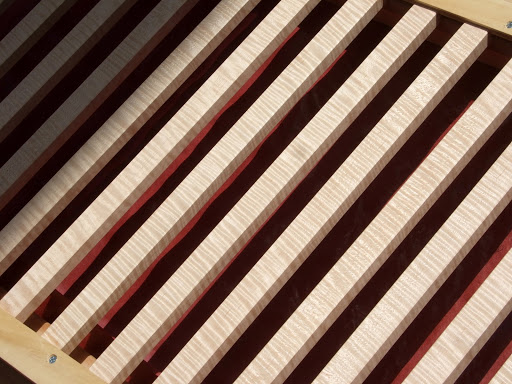
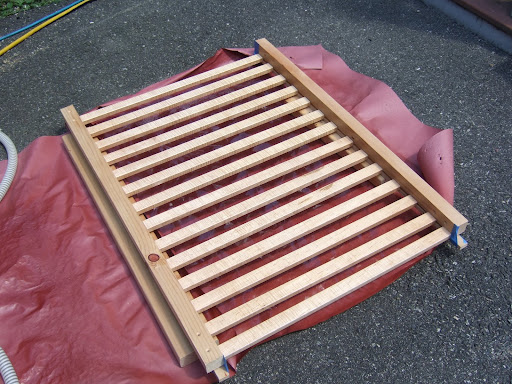
All in all I'm pretty happy with the results. Look at that grain! I'll probably sand them again and add two more coats tomorrow -- just because.